Hazardous Waste Operations and Emergency Response (HAZWOPER) training requirements were set in 1990 by the U.S. Occupational Safety and Health Administration (OSHA) in consultation with U.S. Environmental Protection Agency (EPA), the U.S. Coast Guard (USCG), and the National Institute for Occupational Safety and Health (NIOSH).
You must determine if your company falls under the OSHA HAZWOPER standard or if you are subject to any of the 28 OSHA Plan States, which are state-level regulatory agencies that implement and enforce HAZWOPER regulatory programs. State-level programs often exceed federal regulations.
OSHA & State HAZWOPER Requirements
OSHA HAZWOPER training requirements protect workers at three different levels:
1. General site workers at contaminated sites
2. Emergency responders
3. People who work at hazardous waste treatment, storage, and disposal facilities
Within these three categories are various job functions and training requirements.
NET offers HAZWOPER certification for the different job functions in each of these levels. Our online training courses are OSHA accepted and were reviewed by an OSHA official who helped draft the first HAZWOPER regulations.
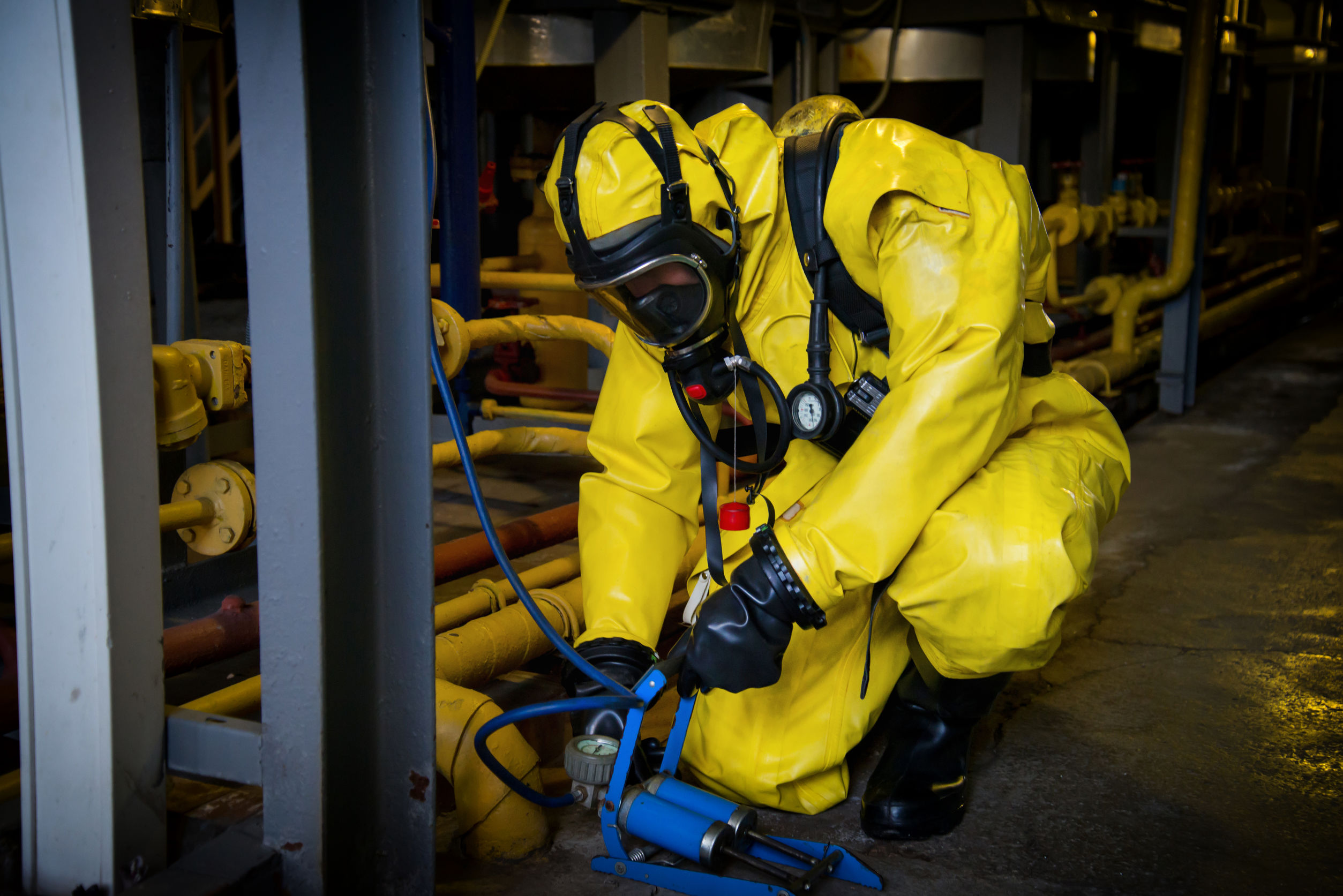
General Site Workers at Contaminated Sites
Contaminated sites are placed on the National Priority List (NPL) by the U.S. Environmental Protection Agency (EPA) and are scheduled for clean-up. The responsible party, as identified in the EPA regulations, usually the site owner or past occupant, must pay for the clean-up cost. This category represents the largest number of people required to be HAZWOPER certified.
Emergency Responders
You can find the minimum HAZWOPER training hours and required competencies for first responders under 29 CFR 1910.120 (q)(6)(ii). Training that is relevant to the required competencies counts toward the minimum time requirement, even if the training is provided as a separate course. For example, training on HAZWOPER Personal Protective Equipment (PPE) that will be used during patient decontamination activities may be applied toward the 8-hour minimum first responder operations level training requirement, regardless of whether the training is conducted as part of a specific HAZWOPER training course or as part of another training program.
Hazardous Waste Treatment, Storage, and Disposal Facilities (TSD) Workers
Workers involved in hazardous waste operations must complete 24-Hour HAZWOPER training and an associated 8-Hour HAZWOPER Refresher. This work typically consists of managing and handling Resource Conservation and Recovery Act (RCRA) hazardous wastes.
HAZWOPER Training Requirements by Job Function
Operation | Initial Training | Annual Refresher Training | Citation 29 CFR 1910.120 | ||
Site Clean Up Operations | |||||
Site Worker | 40-Hour HAZWOPER with three days of field experience | Register Now | 8-Hour HAZWOPER | Register Now | (e)(3)(i) |
Occasional Site Worker | 24-Hour HAZWOPER with one day of field experience | Register Now | 8-Hour HAZWOPER | Register Now | |
Manager or Supervisor | 40-Hour HAZWOPER with three days of field experience and 8 hours of supervisor training | Register Now | 8-Hour HAZWOPER | Register Now | |
TSD Facilities | |||||
Site Worker | 24-Hour HAZWOPER | Register Now | 8-Hour HAZWOPER | Register Now | (p)(7)(i) |
Emergency Response | |||||
First Responder Awareness | Competency-based; no hourly requirement | Register Now | Competency-based; no hourly requirement | Register Now | (q)(6)(i) & (q)(8) |
First Responder Operations | 8-Hour HAZWOPER | Register Now | Competency-based; no hourly requirement | Register Now | (q)(6)(ii) &(q)(8) |
HAZMAT Technician | 24-Hour HAZWOPER | Register Now | Competency-based; no hourly requirement | Register Now | (q)(6)(iii) &(q)(8) |
HAZMAT Specialist | Technician Level competencies | Register Now | Competency-based; no hourly requirement | Register Now | (q)(6)(iv) &(q)(8) |
Incident Commander | 24-Hour HAZWOPER equal to first responder operations competencies | Register Now | Competency-based; no hourly requirement | Register Now | (q)(6)(v) &(q)(8) |
Site Clean Up Operations | ||||||
Site Worker | ||||||
|
||||||
Occasional Site Worker | ||||||
|
||||||
Manager or Supervisor | ||||||
|
||||||
TSD Facilities | ||||||
Site Worker | ||||||
|
||||||
Emergency Response | ||||||
First Responder Awareness | ||||||
|
||||||
First Responder Operations | ||||||
|
||||||
HAZMAT Technician | ||||||
|
||||||
HAZMAT Specialist | ||||||
|
||||||
Incident Commander | ||||||
|
Frequently Asked Questions:
1. What is the training sequence for Emergency Response Workers?
The required training for Emergency Response Workers is HAZWOPER First Responder Operations (FRO) Annual Refresher, HAZMAT Specialist 29 CFR, and 8-Hour HAZWOPER Incident Command. The Emergency Responder training sequence also includes any needed HAZWOPER annual refreshers depending on the time frame.
2. Who needs the 40-Hour HAZWOPER Training?
A person who works in an environment where there is the potential for exposure to hazardous substances at or above permissible exposure limits. This can include clean-up operations or operations involving hazardous substances at the workplace, and the storage, treatment, or disposal of hazardous substances, as well as emergency response operations.
3. What are the training requirements for general site workers at contaminated sites?
General site workers will be required to complete either the 40-Hour or 24-Hour HAZWOPER course. Once that is completed, the next step is to complete any site-specific training that is directed by the employer. Finally, each year, workers must complete the 8-Hour HAZWOPER refresher annually. The course was developed to meet annual HAZWOPER refresher requirements (re-certification) for workers conducting clean-up operations at contaminated sites.
4. What training is required for hazardous waste treatment, storage, and disposal facilities?
Any RCRA TSDF workers must complete the 24-Hour HAZWOPER course and then perform any required site- specific training that is administered by the employer. Once that is completed, an 8-Hour HAZWOPER refresher on an annual basis will be required to maintain the HAZWOPER certificate.
5. How has the 40-Hour HAZWOPER course been updated?
The course has been fully revised and reorganized and features exceptional content containing current research, standards, and technology. The self-paced training is interactive and fully narrated with thorough explanations and check point questions throughout to ensure comprehension. Click here to learn more >>>